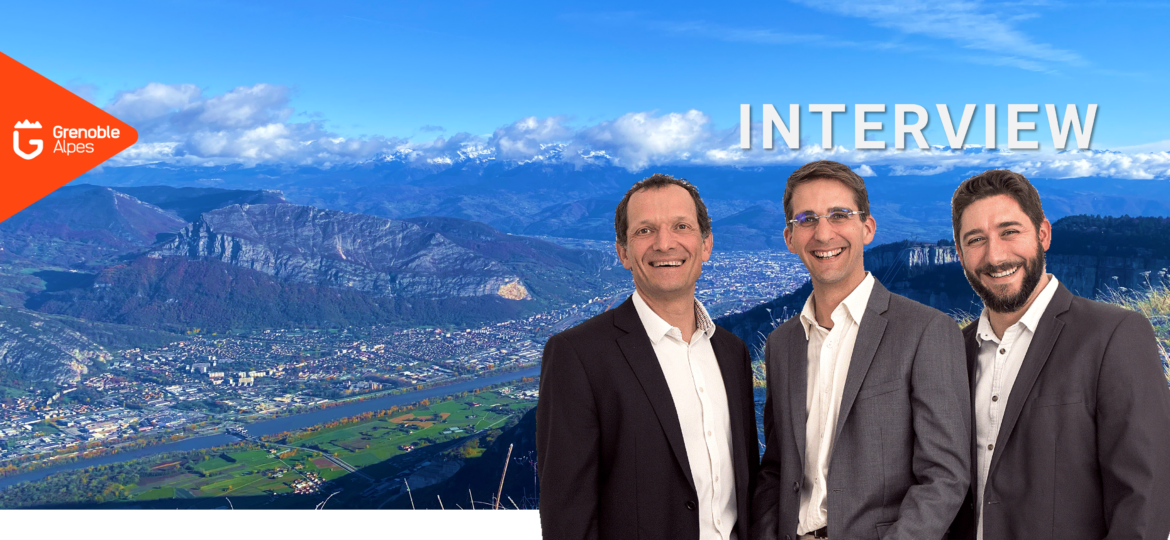
président et co-fondateur de WATTALPS
Notre vraie valeur ajoutée et notre innovation est dans le fait de savoir comment assembler les cellules pour en faire des modules puis ensuite des packs intégrant notre système de refroidissement, et notre système de gestion des batteries…
En termes d’industrialisation, on est en mesure de produire 20 et 25 MWh de batteries par an, c’est déjà une production conséquente, autrement dit c’est l’équivalent de 1 000 batteries d’une minipelle de 2,5 tonnes …
Quelle est l’activité de Wattalps et quels marchés avez-vous ciblés ?
Wattalps est spécialisée dans la fabrication de pack batteries de haute performance. Nous produisons et commercialisations des pack batteries de petites et moyennes séries destinés à des applications mobiles très exigeantes : engins industriels ou agricoles, engins de construction, camions hybrides, véhicules municipaux. Ces applications sont très exigeantes en termes de performance des batteries : elles doivent être à la fois puissantes, pour des engins et des opérations lourdes, et fonctionner sur des temps d’utilisation longs, les engins étant utilisés de manière quasi continue. Nous travaillons aussi sur un autre type d’application, les voitures de course électriques, à la fois pour relever le défi de la performance technologique dans un environnement encore plus exigeant et particulier, et pour des raisons d’image de marque et marketing. Ce n’est pour l’instant pas notre marché cible. Notre métier est donc d’acheter des cellules puis d’en faire des modules, puis des packs complets innovants c’est-à-dire très performants, réutilisables, démontables et recyclables. Nous ne sommes clairement pas positionnés sur les très grandes séries automobiles comme Verkor, ni sur l’aéronautique comme Limatech. D’autres secteurs se montrent également intéressés par notre technologie : le maritime, la logistique aéroportuaire, le stockage stationnaire. Nous les aborderons dans un deuxième temps, car ces secteurs ont leurs propres spécificités qui impliquent d’autres caractérisations technologiques, industrielles, et d’autres réseaux de commercialisation, ce qui suppose d’avoir une maturité d’entreprise plus importante.
Comment a commencé l’aventure Wattalps ?
WATTALPS est une entreprise co-fondée par trois associés, Jean-Noel Carminati, ancien du CEA, Manuel Ronco ex salarié de Aixam-Mega, entreprise de l’industrie du véhicule électrique, et moi-même, également ancien au CEA.
Au CEA nous travaillions sur l’amélioration de la performance des batteries – vaste domaine de recherche – et en 2013 on a commencé à développer un nouveau système de refroidissement par immersion qui a donné lieu deux ans après en 2015 au concept innovant de Wattalps. Le CEA nous a accordé un financement pour élaborer un démonstrateur, ou modèle réduit, qui nous a permis de mesurer et de prouver les performances de notre nouveau concept. Cela a surtout permis au CEA de gagner un contrat avec Oscaro.com. Oscaro a financé le démonstrateur à échelle 1, que nous avons finalisé en 2018. Là aussi, avec le CEA, nous avons confirmé l’impact réel de notre innovation technologique sur la performance, la durée de vie et la sécurité des batteries. Nous avons alors créé la société Wattalps pour se lancer dans l’industrialisation. Oscaro pouvait utiliser la technologie dans l’automobile, là où nous l’utilisions sur des applications et des marchés de niche. Aujourd’hui nous notre technologie est protégé par 7 brevets, 3 brevets sous licence du CEA et 4 en propriété industrielle et intellectuelle propre à Wattalps.
Quelle est le cœur de votre innovation de rupture ?
La performance et la durée de vie des batteries est très liée à leur température. D’une manière générale la chaleur excessive (tout comme le froid excessif) ont un grand impact sur leur performance, leur durée de vie et leur sécurité. Il y a une limite de température au-delà de laquelle la recharge devient impossible, et une 2ème limite de température (bien plus élevée) où on entre dans des risques de départ de feu. La chaleur est fonction de l’usage que l’on fait des batteries et aussi des conditions extérieures. Dans un contexte climatique général où les températures sont de plus en plus chaudes, maintenir la température d’une batterie devient un enjeu majeur. L’innovation de rupture de Wattalps repose sur deux caractéristiques technologiques qui garantissent un très haut niveau d’homogénéité de température de la batterie : c’est à la fois un système de refroidissement par immersion dans un liquide biodégradable, isolant électrique, non toxique et non inflammable, et une architecture brevetée développée en collaboration avec des salariés du CEA spécialistes de la thermique et d’autres spécialistes des batteries. WATTALPS se fournit en cellules et en liquide de refroidissement, et assemble le tout pour former des batteries « plug and play » pour ses clients. Notre vraie valeur ajoutée et notre innovation est dans le fait de savoir comment assembler les cellules pour en faire des modules puis ensuite des packs intégrant notre système de refroidissement, et notre système de gestion des batteries. Les cellules sont complètement immergées dans le fluide ; c’est le meilleur moyen de maitriser leur température. Cette immersion permet d’homogénéiser et de maitriser la température de la batterie, avec des écarts de température inférieurs à 2 degrés sur l’ensemble de la batterie. Un de nos gros clients spécialisés dans les engins agricoles hybrides nous a confirmé qu’il n’avait jamais vu, au cours de ses tests des batteries avec un aussi bon comportement sur le plan thermique. On démontre aujourd’hui un niveau de performance et de durée de vie inégalé par les solutions concurrentes.
La sécurité de nos batteries repose quant à elle sur deux piliers : la conception des batteries comme je viens de l’expliquer, et le système de gestion des batteries (le BMS – Battery Management System). Wattalps a également développé une électronique de gestion qui est aujourd’hui au meilleur niveau de sécurité du marché, calé sur les standards les plus exigeants de l’automobile. En partant d’un prototype fonctionnel, cela nous a pris 6 ans supplémentaires de développement pour obtenir en 2023 la certification ISO 26262 sur la sureté de fonctionnement de notre système de batteries modulaires, dont 4 ans d’évaluation par une société indépendante. En 2023, nous avons obtenu deux autres certifications : l’IEC 62619 pour la sécurité des batteries industrielles auprès de l’un des 5 laboratoires accrédités à en Europe pour certifier une batterie selon ce standard et la certification ISO 9001 pour l’organisation industrielle. Elles attestent du très haut niveau de sécurité : en usage normal, nos batteries ont une probabilité de défaillance déclenchant un problème de sécurité toutes les dix-millions d’heures de fonctionnement. Nous sommes la seule entreprise au monde à avoir atteint ce niveau de certification pour des batteries refroidies par immersion. Nous en sommes très fiers, c’est un pas très important pour Wattalps et pour l’équipe, qui nous permet de sécuriser nos clients et nos partenaires et d’entrer plus sereinement dans la phase de « passage à l’échelle » et d’accélération de notre industrialisation.
En quoi votre technologie se distingue des autres technologies disponibles ?
Le refroidissement et le maintien de la température des batteries sont les éléments clé de la performance, de la durée de vie et de la sécurité des batteries. Il y a deux solutions technologiques qui sont utilisées aujourd’hui sur le marché, le refroidissement par air et celui par eau, mais toutes deux présentent des inconvénients. Dans ces deux solutions, les flux permettent de refroidir la batterie mais ils se réchauffent en même temps qu’ils circulent : les écarts de température entre les cellules qui sont refroidies en premier grâce au flux et celles refroidies en dernier peuvent atteindre jusqu’ à 30 degrés avec un système de refroidissement à air et 14 degrés avec un système de refroidissement à eau. La solution technologique de Wattalps nous permet de limiter ces écarts de température à 2° seulement. C’est notre avantage et notre atout majeur. Je le disais tout à l’heure, lorsqu’on maitrise la température des batteries, on maitrise la performance et la durée de vie. Dans un environnement à -10°C une batterie voit son autonomie divisée par deux et dans un environnement à plus de 45° elle vieillit plus de deux fois plus vite. Une batterie qui atteint plus de 45 degrés est une batterie impossible à recharger. Vous voyez bien que dans ces conditions un système de refroidissement qui assure des écarts de 14 degrés entre les cellules qui composent la batterie est un système qui impacte très fortement la performance et l’autonomie. On pourrait compenser ces effets en jouant sur la taille des batteries, mais typiquement dans le cas d’un engin industriel qui fonctionne 8h par jour et qui demande une forte puissance en continue, la batterie serait tout simplement surdimensionnée (trop lourde, trop volumineuse et trop couteuse).
Vous êtes en phase d’industrialisation de votre produit : à quelle étape en êtes-vous ?
En termes d’industrialisation, on est en mesure de produire 20 et 25 MWh de batteries par an, c’est déjà une production conséquente, autrement dit c’est l’équivalent de 1 000 batteries d’une minipelle de 2,5 tonnes.
Dans notre process industriel, il reste encore un nombre élevé d’opérations manuelles même si une partie du procédé est robotisée (machine de soudure automatiques, bancs de test automatique, ..) . L’automatisation est un des axes importants de notre développement dans les deux ans qui viennent. Aujourd’hui Wattalps emploie 15 à 20 personnes, nous serons environ 30 en fin d’année, et nous prévoyons d’être une centaine de personnes dans 5 ans. Nous sommes sur des productions de petite voire moyenne série, sur un marché de niche avec des exigences très élevées.
Notre croissance est progressive : tous nos clients ont des projets avec nous qui durent minimum 3 à 4 ans et souvent jusqu’à 7 ans. Ils commencent par tester et valider les premières batteries sur leurs engins, pour passer ensuite en pré-série puis en série. Nos premiers clients ont validé et commandé leurs premières pré-séries et souhaitent déjà équiper d’autres gammes de machines avec nos produits. Cette approche nous permet de créer des liens de confiance très important avec nos clients. On entre progressivement dans une phase de contrats de fournitures régulières.
A ce jour, nous avons déjà livré ou sommes en cours de livraison dans 8 pays européens et très prochainement aux Etats-Unis. On couvre divers segments (construction, agriculture, industrie … ) et on a un large panel de clients : des grands groupes qui font plusieurs milliards d’€ de chiffre d’affaires mais aussi des ETI ou des PME et des projets plus innovants comme celui des voitures de course. Notre objectif est d’être avec chaque client au rendez-vous de la performance, de la durée de vie et de la sécurité des produits qu’on leur propose. On a besoin de leurs retours, et c’est comme cela qu’on peut envisager notre croissance de manière durable.
Pouvez-vous nous dire comment vous avez anticipé la problématique du recyclage de vos batteries ?
Merci de ma poser la question. C’est en effet l’autre spécificité très importante de notre activité, le recyclage et la seconde vie de nos batteries. Dès le démarrage de Wattalps, nous l’avons anticipé dans la conception même du produit en prenant conseil auprès d’experts du recyclage. Nos batteries sont totalement démontables afin de séparer les composants électroniques des autres éléments qui sont recyclables. Et grâce à notre système de modularité et aux connecteurs qui sécurisent les opérations de démontage, nos batteries sont aisément réparables et simples à réutiliser. Nous avons d’ailleurs obtenu le label Solution efficiente de Solar Impulse qui est l’un des premiers labels pour les entreprises à impact positif qui allient protection de l’environnement et viabilité financière.
Les batteries Wattalps sont conçues pour des cas d’usages avec des besoins de performance très élevés mais lorsque, par usure, elles ne pourront plus répondre à ce niveau d’exigence, en particulier leur perte d’autonomie, il sera possible de les reconditionner pour les mettre dans des applications moins exigeantes, comme par exemple les chariot-élévateurs ou les groupes électrogènes. Certains de nos clients ont des machines haute performance mais aussi des machines d’entrée de gamme. On va donc pouvoir adresser le même marché pour la seconde vie de nos batteries. Aujourd’hui nos batteries sont tellement performantes et durables que l’on a pas pu encore tester leur seconde vie avec nos clients. Mais c’est un axe de développement très important pour nous, avec un impact environnemental réel et qui est tiré par la nouvelle directive européenne qui est entrée en vigueur en juillet 2023 (le règlement (UE) n°2023/1542 du Parlement européen et du Conseil du 12 juillet 2023 relatif aux batteries et aux déchets de batteries). Cette directive renforce les règles de durabilité, de sécurité et de marquage des batteries ainsi que les règles relatives à la seconde vie des batteries. Elle va progressivement imposer à toutes les entreprises qui mettent des batteries sur le marché de les collecter en fin de vie. Nos clients qui fournissent des engins complets avec des batteries vont devoir collecter les batteries et s’arranger pour les recycler. Plus ils seront face à cette situation plus ils vont comprendre l’intérêt de nos produits. Cette obligation a un effet d’accélération de notre développement c’est certain. On ne manque pas de sujets et d’axes de croissance. Il y a tout une logique de circuit court à concevoir et à mettre en place pour et avec nos clients autour de la seconde main et du recyclage, très surement aussi un modèle d’impact environnemental, de responsabilité social et environnemental. C’est dans l’ADN de l’équipe depuis le début. Ce sera une partie importante de notre réussite.